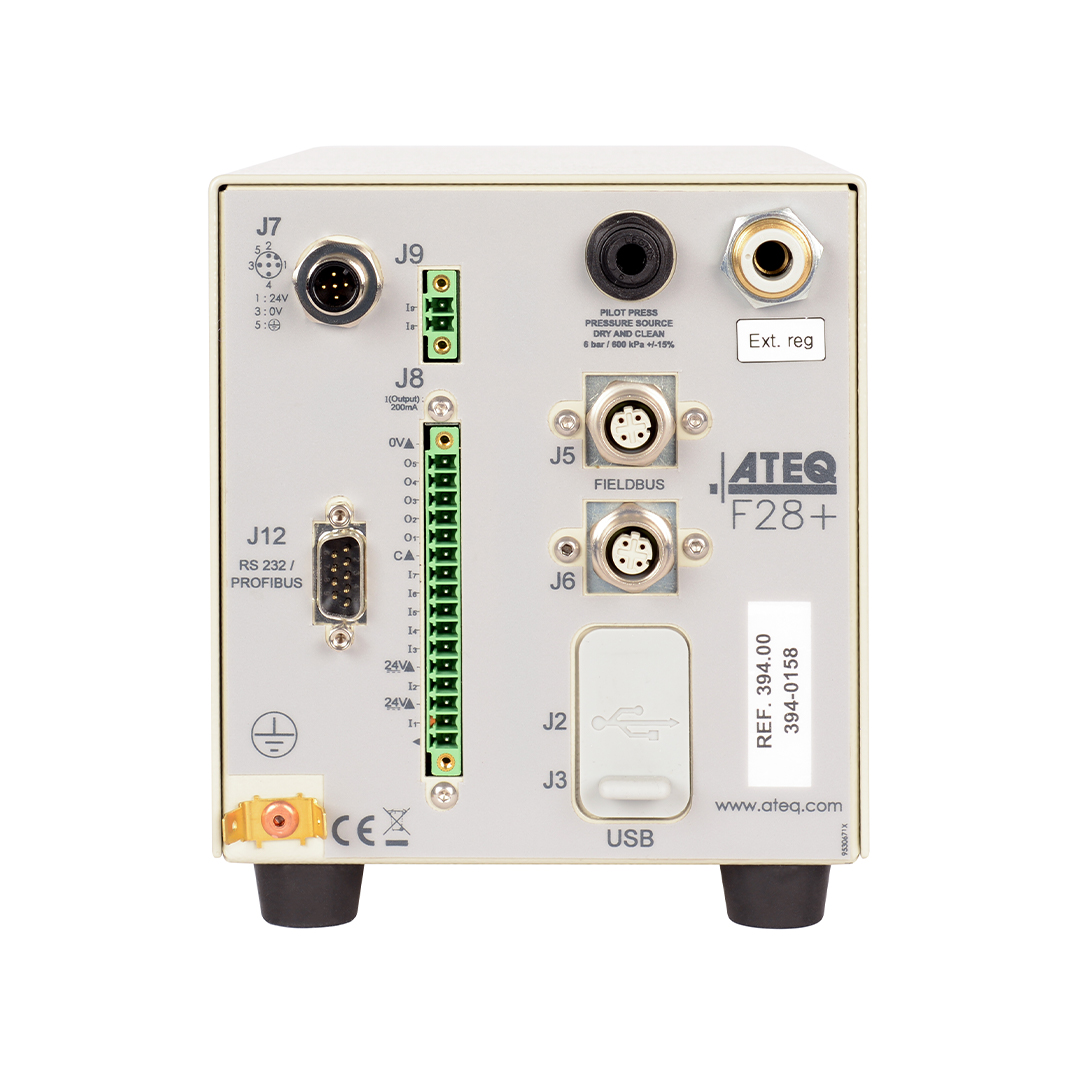

F28+ – COMPACT LEAK TESTER
FOR INDUSTRIAL QUALITY CONTROL
F28+: The new innovative tester, made by ATEQ, elevates the leak test to a whole new level of speed, flexibility and accuracy.
You can easily supervise it with a touch-screen panel + our user friendly interface: winateq 300.
Adapted for manual, semi-automatic and fulled automated leak testing, the F28+ has a full range of specifications at a very competititve price
F28+ : APPLICATIONS
Automotive, domestic appliances, medical, aeronautic, defense, fluid and electrical components, food and cosmetic packaging…
F28+ : FEATURES
• Differential pressure decay leak measurement: vacuum to 20 bar
• Multi-test leak tester
• 128 programs
• Fully integrated electronics and pneumatics
• Flexible communication format: Bar code reader, RS232, USB
• Date storage on internal memory or USB key
TEST MODES :
• ∆P (Pa, 1/10 Pa)
• ∆P/t (Pa/s, 1/10 Pa/s)
• Flow units (sccm, mm3/s, cm3/s, cm3/min, cm3/h…)
• Blockage test
• Burst test
• Sealed components test
• and others, depending on your applications
ENVIRONMENT :
ROHS standard
MEASUREMENT CHARACTERISTICS :
F28+ Demo interface
F28+ Demo interface
F28+ : SPECIFICATIONS
PRESENTATION
- Weight : around 3.5 Kg
PHYSICAL
- Dimensions : (in mm) H 157.10 x W 298.90 x D 135.80g
- ELECTRICAL SUPPLY
- 24 V DC / 1.6 A4VDC/2A or 100-240VAC/50W
- AIR SUPPLY
- Clean and dry air required
- Air quality standard to be aplied (ISO 8573-1)
- Test pressure input, need an external regulator
- TEMPERATURE
- Operating : + 5°C at + 45°C
- Storage : 0°C at + 60°C
F28+ : OPTIONS
• 9 inputs / 5 outputs
• Option Fieldbus: profibus, devicenet, profinet, Ethernet/ IP, Ethercat network, Mobus RTU
• 6 x 24 V programmable outputs for external automation
• Electronic regulation
• 1 pneumatic output for automation
F28+ : FACTSHEETS
Detailed information about the F28+ including features, specifications, etc.
F28+ : TECHNOLOGY
By far the most popular technology, differential pressure decay uses a reference volume to test your part. This helps compensate for any ambient pressure or temperature variations as they occur on both parts simultaneously.
Only a leak on the test part will result in a movement of our transducer’s membrane.
The second advantage of this method is that the accuracy does not drop with the test pressure as the transducer is measuring pressure differences between the two circuits, as opposed to the traditional pressure decay technology that measures pressure drops against the atmosphere.
Direct measurement principle
The part under test 3 and the reference part 5 are filled to an identical pressure. A differential sensor 4 measures the pressure variation between the part under test 3 and the reference part 5. In some applications, the reference part can be replaced by a cap.
Desensitized test
This mode is used for the measurement of large leaks, when the reject level required is above the full scale of the differential sensor.
The test pressure is applied to the input of the part under test 3. The measurement is performed by the pressure sensor 2.
Other type of tests are available in option